Published 11th Jan 2024
Troubleshooting Lamination Issues: Expert Solutions for a Flawless Finish
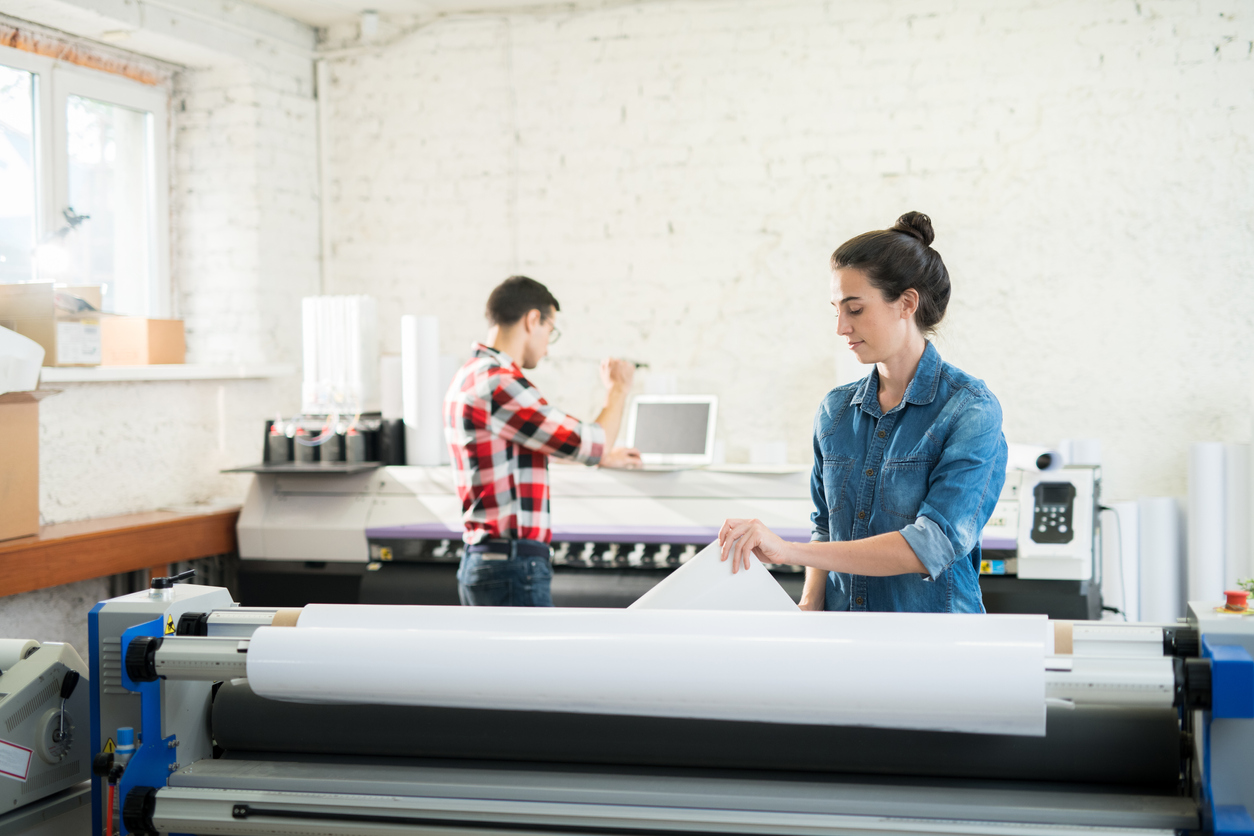
Laminating is an essential part of producing long-lasting wide format printed graphics. They provide a protective layer and enhance the visual appeal of materials such as posters, vinyls, banners, and signs. But unfortunately, they also come with a set of potential lamination issues.
In this blog, we’ll explore some common issues encountered during laminating and give you some practical solutions to ensure a flawless finish every time.
Bubbles or Wrinkles
One of the most frustrating problems in laminating is the appearance of bubbles or wrinkles. These imperfections can mar the visual appeal of the material, and many clients will reject these graphics outright.
To overcome these lamination issues, start by ensuring that your material is laid out flat and smooth before the laminating process. Adjust the laminator’s pressure settings to reduce the chances of air bubbles forming.
Uneven Lamination
Uneven lamination is another common concern, often caused by inconsistent pressure or temperature settings on the laminator.
To address this, check and adjust the pressure settings based on the thickness of the material being laminated. It’s crucial to maintain a consistent temperature or pressure level across the entire width of the laminator.
Fine-tuning these settings will help you achieve a smooth and even lamination.
Peeling or Delamination
Peeling or delamination occurs when there is inadequate adhesion between the laminate and the material.
This can be resolved by ensuring that the laminating film is compatible with the material. Check and adjust the temperature settings on the laminator to match the specifications of the laminating film. It is also important to make sure that the print has had sufficient time to outgas before laminating.
If needed, a slight increase in temperature can improve adhesion. Allow the material to cool properly after lamination to prevent premature peeling.
Jamming or Misfeeds
Jamming or misfeeds can disrupt the laminating process, leading to uneven lamination and potential damage to the material.
To avoid this issue, take extra care in aligning the material before feeding it into the laminator. Ensure that the material is loaded straight and free of any wrinkles or folds.
If misfeeds persist, inspect the laminator for any obstructions and clear them promptly.
Cloudy or Hazy Finish
A cloudy or hazy finish can diminish the clarity and vibrancy of your laminated material. This issue is often a result of incorrect temperature settings or the use of low-quality laminating film.
To combat this problem, ensure that the laminator is set to the recommended temperature for the chosen laminating film. Investing in high-quality laminating film can significantly improve the transparency of the final product.
Adhesive Residue
Adhesive residue left on the laminated material can be unsightly and compromise its overall quality.
Regularly clean the rollers and plates of your laminator to prevent the buildup of excess adhesive.
Additionally, allow sufficient time for the material to cool after lamination. Proper cooling helps the adhesive set and reduces the chances of residue.
Edge Sealing Issues
Inadequate sealing at the edges of laminated materials can lead to peeling and reduced durability.
Adjust the pressure settings on your laminator to ensure proper edge sealing. After lamination, carefully trim the material to prevent it from peeling at the edges.
This attention to detail can make a significant difference in the longevity of the laminated product.
Wrinkled Edges
Wrinkled edges can be a result of tension on the material during lamination.
To address this, ensure that the material is fed into the laminator flat and evenly. If your laminator has tension adjustment features, use them to achieve optimal results.
Silvering
Silvering refers to the appearance of tiny silver-like streaks or specks in the laminated material, creating a reflective or metallic effect. This phenomenon is often caused by air or adhesive voids between the laminating film and the substrate.
To minimise silvering, follow proper material preparation procedures, use appropriate temperature and pressure settings, opt for high-quality laminating film, apply the film slowly and evenly, consider a laminator with air evacuation features, and allow proper post-heating and cooling.
In conclusion, mastering the art of laminating involves addressing these common lamination issues with precision and care. By understanding the causes and implementing the suggested solutions, you can elevate your laminating process and consistently achieve professional, picture-perfect finishes. Remember to refer to the manufacturer’s guidelines for your specific laminator and laminating film, and conduct regular maintenance to keep your equipment in optimal condition.
If you have other tips on how to fix these issues, feel free to share them with us and we can update this article for all to benefit from it!
Latest blog posts
View all posts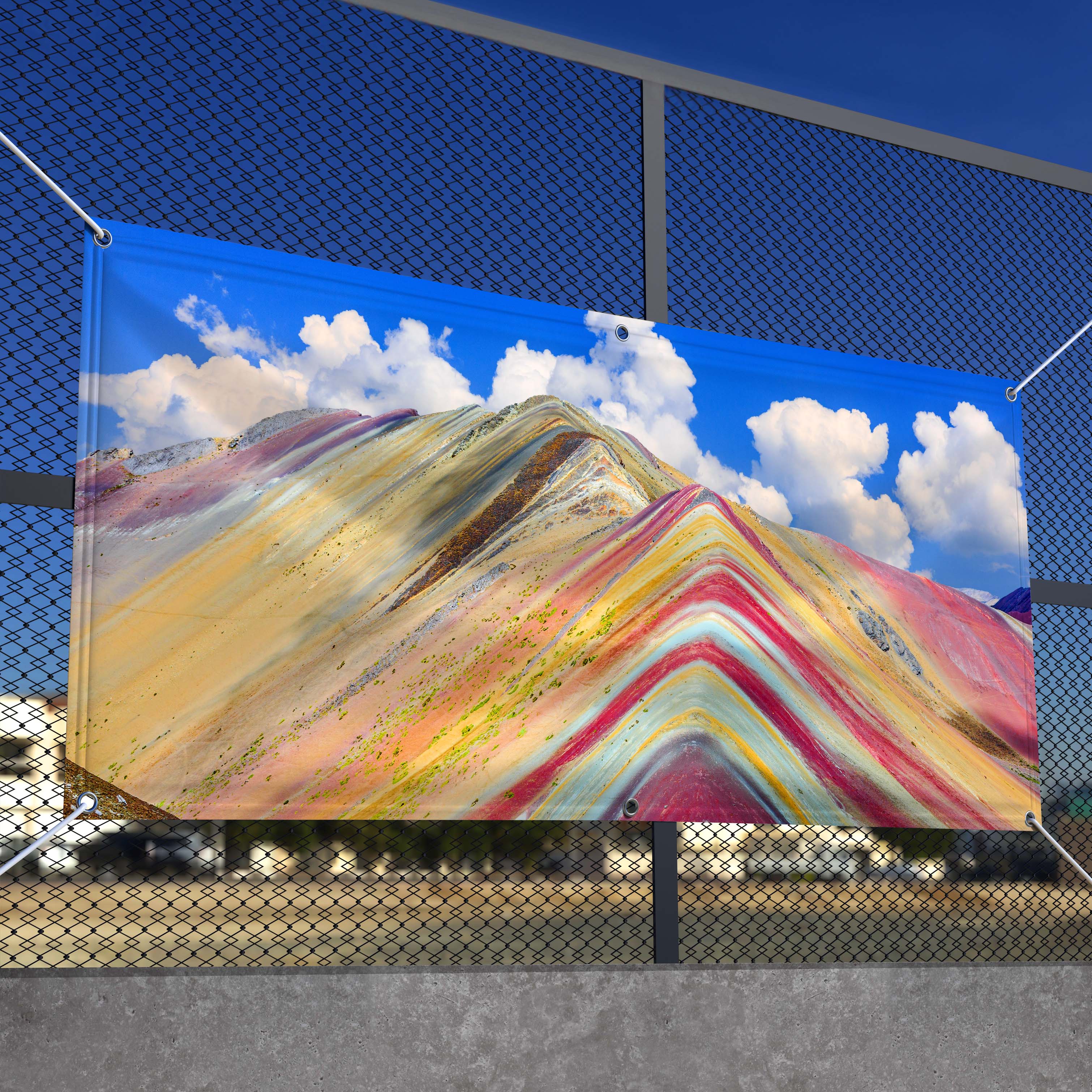
5th May 2025
Common Challenges with PVC Free Vinyl and How to Overcome Them
PVC free vinyl is becoming an increasingly popular choice for businesses looking to reduce their environmental impact [...]
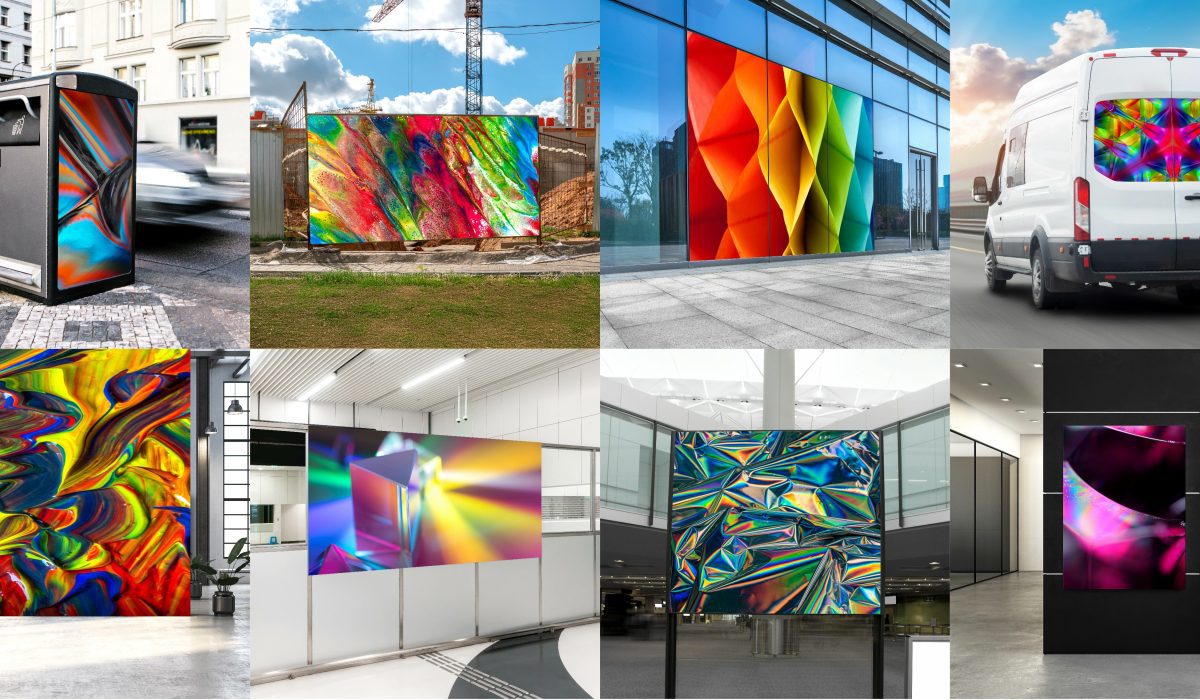
15th April 2025
Innotech Expands Range of General Formulation Self-Adhesive Vinyls
After becoming the exclusive UK distributor for General Formulations last year, Innotech are now offering the new GF [...]
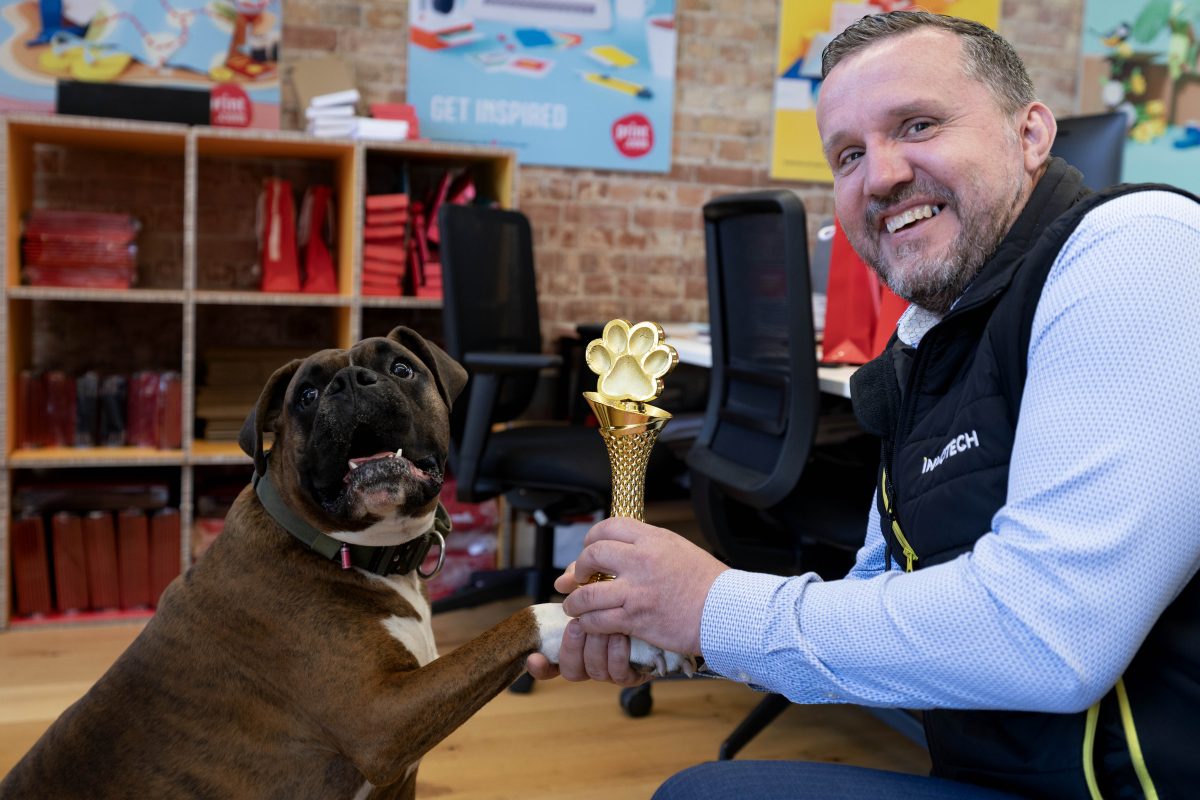
11th April 2025
Gary from Print.com is Pets in Print Trophy winner
Innotech Digital and Display announce the winner of this year’s Pets in Print competition is Gary from Print.com. He [...]